What Is a Turbine Flow Meter?
A Turbine Flow Meter is a precise and reliable type of flow sensor that is installed in the direction of fluid flow and is capable of measuring the flow rates of liquids and gases. It contains a rotor, which is a blade assembly that spins as fluid passes through it. As the fluid flow's velocity increases, the rotor spins faster. Measuring the rotational speed of the rotor determines the volumetric flow rate.
Technical Specifications of Turbine Flow Meter
The Turbine Flow Meter was invented by Reinhard Woltman and is a precise and reliable flow meter for measuring the flow rates of liquids and gases. The turbine flow meter consists of a flow tube with end fittings and a free-spinning multi-blade magnetic rotor installed inside the device. The rotor, located on a shaft, rotates in the direction of the fluid flow.
How Does a Turbine Flow Meter Work?
The turbine's impeller is the only moving part of the flow meter and is immersed in the flowing fluid. As the fluid flows through, it engages the impeller, causing it to rotate at a speed proportional to the fluid flow's velocity. The impeller's rotational speed generates an electrical signal (a sinusoidal AC waveform). The shaft's rotation is measured either mechanically or by detecting blade movement and is sensed magnetically, generating pulses.
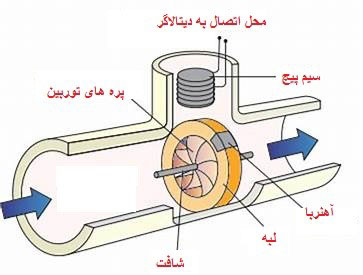
The sensor of the turbine flow meter is positioned outside the fluid path and is protected from the fluid's effects. As the fluid flow's velocity increases, the impeller rotates more rapidly, producing more pulses. These signals are processed by a transmitter to calculate the volumetric flow rate. The transmitter and sensor system can operate in both the forward and reverse flow directions.
Installation Instructions for Turbine Flow Meter
Turbine flow meters are used for measuring the flow of clean fluids because, when used with dirty fluids, the turbine blades can experience wear and erosion. However, turbine flow meters are suitable for fluids that contain fine particles. To prevent this, a strainer (filter) can be installed upstream of the flow meter to prevent fine particles from entering.
It should be noted that the size of the flow meter should be within a certain range compared to the pipe size, and the flow meter should be installed in the direction of fluid flow. There should be no obstructions in the flow path, with a minimum of 10 times the pipe diameter before and 5 times the pipe diameter after the flow meter. Valves and fittings should be placed downstream of the flow meter.
Applications of Turbine Flow Meter
Turbine flow meters are used for measuring flow in relatively clean fluids, liquids, and consumable fluids up to 24 inches in size. In the measurement of fluid flow rates, the materials of various parts of the flow meter, including the body, rotor, bearings, fittings, etc., should be selected to be resistant to fluid corrosion.
Additionally, turbine flow meters measure the flow rates of liquids, gases, and vapors inside pipes, such as hydrocarbons, cooling liquids, chemicals, industrial gases, air, and more. Turbine flow meters are used in power plants, chemical industries, food and pharmaceuticals, water and wastewater treatment, metals and mining, paper production, and oil and gas applications.
Advantages of Turbine Flow Meter
Low Cost
Cost-Effective Maintenance
Smaller Dimensions
Linear
High Reproducibility
Dual-Pulse Output
Weaknesses of Turbine Flow Meter
Suitable for Single-Phase Flows
Dependent on Fluid Density
Low Operational Range in High-Viscosity Fluids
Dependent on Upstream Flow Profile
Bearing Wear
Not Suitable for Accurate Steam Flow Measurement